Proper maintenance of equipment is crucial for ensuring longevity, minimizing downtime, and maintaining operational efficiency. Whether you’re managing industrial machinery, vehicles, or tools, adopting proactive maintenance practices can prevent costly repairs and replacements. Below, we delve into practical tips for preventing rust, maintaining cleanliness, and utilizing cutting-edge smart diagnostic tools to keep your equipment in top condition.
Preventing Rust: The Silent Equipment Killer
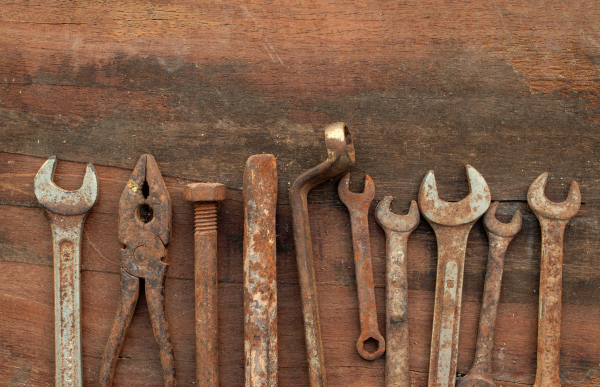
Rust is one of the most pervasive challenges in equipment maintenance. Left unchecked, it can weaken metal structures, degrade performance, and lead to expensive repairs. The key to tackling rust is prevention through diligent care and the right tools. Here’s how to prevent rust effectively:
- Use Protective Coatings
- Apply rust-resistant paints, oils, or sprays such as Rust Grip®, which can be applied directly over rust without sandblasting.
- For heavy-duty equipment, consider products like POR-15 Rust Preventive Coating for exceptional rust protection.
- Control the Environment
- Store equipment in dry, temperature-controlled areas to minimize exposure to moisture and humidity.
- Use dehumidifiers in storage spaces, especially in regions prone to high humidity.
- Regular Cleaning and Drying
- Clean equipment after use, particularly if it’s been exposed to water, salt, or harsh chemicals.
- Products like Rust-Oleum Regal Red Enamel Paint can provide rust-preventive coatings while also offering environmental protection.
- Inspect for Early Signs of Corrosion
- Conduct regular visual inspections to identify early signs of rust. Address minor rust issues immediately using sandpaper or wire brushes followed by a rust inhibitor.
- Invest in Rust Prevention Products
- Anti-corrosion sprays and lubricants are critical for specific equipment. For tools and small machinery, silica gel packs in storage containers can help absorb excess moisture.
Keeping Equipment Clean: Maintenance Starts with Hygiene
Keeping equipment clean is more than just about appearances; it directly impacts performance and longevity. Over time, dirt, grease, and grime can accumulate, leading to clogged components, inefficient operation, and even breakdowns. Here’s how to maintain cleanliness:
- Develop a Cleaning Schedule
- Implement a regular cleaning routine based on equipment usage. High-use machinery may require daily cleaning, while less frequently used items can follow a weekly or monthly schedule.
- Choose the Right Cleaning Products
- The choice of cleaning products is equally important. Not all cleaning agents are suitable for every type of equipment. For instance, degreasers work wonders on engines but can corrode delicate parts if used improperly. For painted surfaces, non-abrasive cleaners provide effective cleaning without damaging the finish.
- Pressure Washing for Large Equipment
- It not only saves time but also ensures deep cleaning in hard-to-reach areas. However, the pressure settings must be adjusted carefully to prevent water intrusion into sensitive components.
- Inspect and Replace Filters
- Clean or replace air and fluid filters regularly to prevent clogging and contamination.
- Train Employees on Proper Cleaning Techniques
- Provide training to staff to ensure equipment is cleaned correctly and without causing damage.
Leveraging Smart Diagnostic Tools for Advanced Maintenance
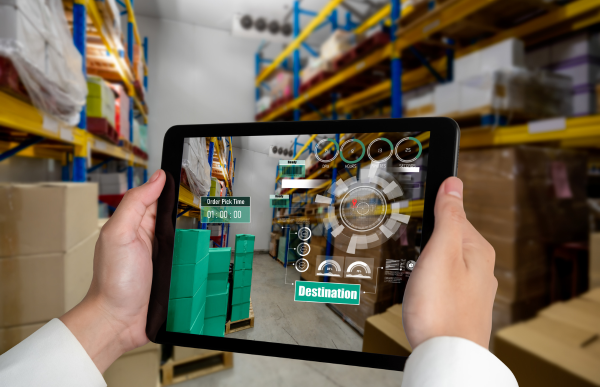
Technology has revolutionized equipment maintenance with the advent of smart diagnostic tools. These tools provide real-time insights and predictive analytics to minimize downtime and optimize performance.
- Integrate IoT-Enabled Sensors
- Products like Augury’s Machine Health Solutions utilize IoT and AI to predict and prevent failures before they occur. These sensors monitor critical parameters such as temperature, vibration, and pressure, sending real-time alerts when abnormalities arise. This technology enables maintenance teams to act swiftly and avoid potential breakdowns.
- Use Predictive Maintenance Software
- Platforms like SMARTdiagnostics® by KCF Technologies analyze historical and real-time data to predict when a machine is likely to fail. This allows teams to plan maintenance during non-critical periods, minimizing operational disruptions.
- Digital Diagnostic Scanners
- For vehicles and complex machinery, use handheld tools like the Smart Machine Checker (SMC), which offers fast, easy-to-understand diagnostics. This user-friendly device generates diagnostic reports in minutes, making it easier to troubleshoot issues without extensive technical training.
- Mobile Maintenance Apps
- Mobile apps for maintenance management, such as UpKeep or Fiix, further streamline operations. These platforms centralize maintenance data, track schedules, and even provide detailed instructions for complex repairs. Some apps integrate seamlessly with IoT devices, enhancing overall efficiency.
- Invest in Augmented Reality (AR) Tools
- AR tools provide visual guides for repair and maintenance procedures, reducing errors and training time.
Building a Proactive Maintenance Culture

Preventing rust, maintaining cleanliness, and leveraging smart diagnostic tools are foundational to effective equipment care. However, the success of these practices hinges on fostering a proactive maintenance culture within your organization.
- Implement Regular Training
- Training employees on proper maintenance techniques ensures consistency and reduces the risk of human error. Regular workshops or refresher courses can familiarize staff with the latest tools and strategies. Additionally, documenting maintenance procedures in clear, step-by-step checklists ensures everyone follows the same standards.
- Document Procedures
- Create detailed maintenance checklists for each type of equipment to minimize human error.
- Track Maintenance Metrics
- Tracking maintenance metrics, such as downtime, repair costs, and equipment lifespan, provides valuable insights into the effectiveness of your strategies. By analyzing this data, you can identify trends and areas for improvement, ensuring continuous optimization.
- Engage in Continuous Improvement
- Finally, encourage feedback from your maintenance team. Frontline workers often have the most practical insights into what works and what doesn’t. By incorporating their suggestions, you can create a more efficient and effective maintenance system.
Effective equipment maintenance combines diligence, strategic planning, and the use of innovative tools. By prioritizing rust prevention with products like Rust Grip®, ensuring cleanliness with non-abrasive cleaning solutions, and leveraging advanced diagnostic tools such as Augury’s Machine Health Solutions, businesses can significantly extend equipment lifespan and reduce costs.
In a competitive environment, staying ahead means not only maintaining your equipment but also optimizing it for peak performance. Begin implementing these strategies today to protect your investment and ensure your operations remain efficient and profitable.