In 2025, the construction industry is undergoing a remarkable transformation, with foam-based building materials emerging as a revolutionary alternative to traditional methods. Foam homes, constructed using insulated concrete forms (ICFs), spray foam, and expanded polystyrene (EPS), offer a sustainable, cost-effective, and highly durable solution to modern housing challenges. As demand for eco-friendly, disaster-resistant, and energy-efficient homes increases, the use of foam is reshaping the way we build.
But what exactly makes foam such a game-changer in home construction? Let’s explore the benefits, technology, and future potential of foam-based homes.
What Are Foam Homes?
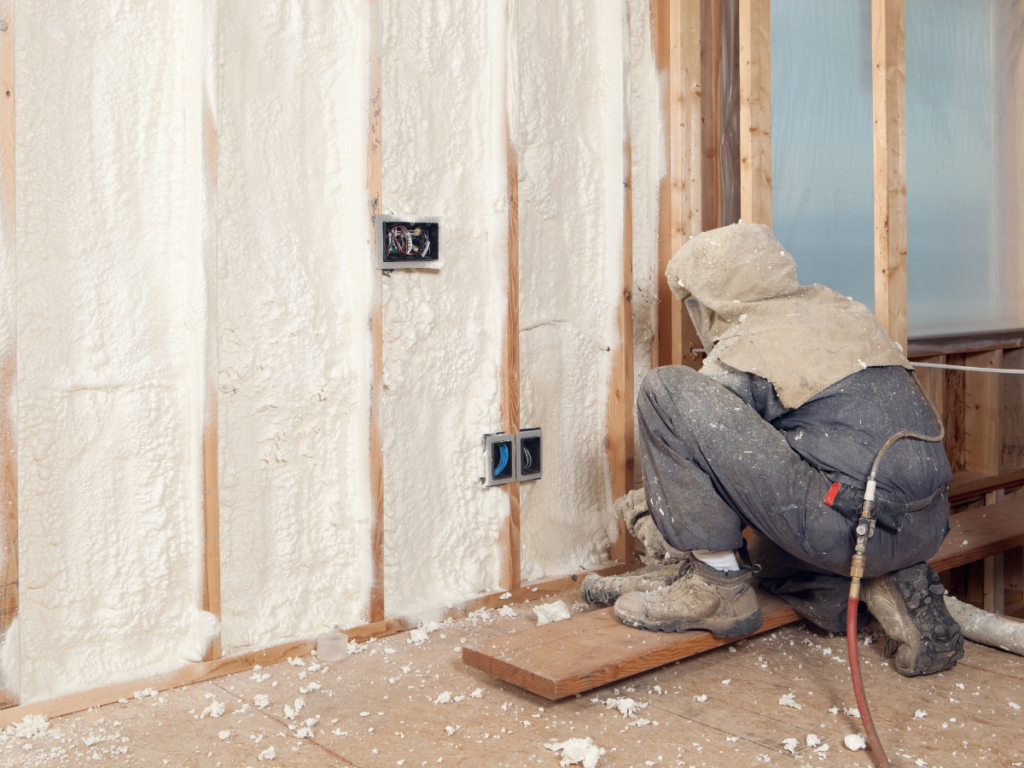
Foam homes refer to structures built using lightweight, high-density foam materials such as insulated concrete forms (ICFs), expanded polystyrene (EPS) blocks, and spray polyurethane foam (SPF). These materials provide excellent thermal insulation, structural integrity, and moisture resistance, making them a viable alternative to traditional wood, brick, or concrete houses.
The technology behind foam-based construction has been around for decades, but recent advancements in manufacturing, sustainability, and climate resilience have made it a more attractive option in 2025.
Types of Foam Used in Home Construction:
- Insulated Concrete Forms (ICFs) – Hollow foam blocks filled with concrete to create walls that are both insulated and structurally sound.
- Spray Polyurethane Foam (SPF) – Used as an insulator that expands to fill walls, roofs, and gaps, improving energy efficiency.
- Expanded Polystyrene (EPS) Blocks – Lightweight, prefabricated foam panels used for walls, floors, and roofs.
- Structural Insulated Panels (SIPs) – Foam core sandwiched between plywood or OSB (oriented strand board) panels, offering superior insulation.
Why Foam Homes Are the Future of Construction
Foam-based construction offers numerous advantages over traditional materials, making it an attractive option for homeowners, developers, and governments seeking sustainable and affordable housing solutions.
1. Energy Efficiency & Cost Savings
One of the most significant benefits of foam homes is their superior insulation properties. Foam materials provide high R-values, meaning they retain indoor temperatures more effectively than wood or brick structures.
- Lower Energy Bills: Foam homes reduce heating and cooling costs by up to 50%, making them an excellent choice for energy-conscious homeowners.
- Reduced HVAC Dependence: The airtight nature of foam insulation minimizes the need for large heating and cooling systems, cutting down energy consumption.
- Sustainable Living: With rising concerns about carbon footprints, foam homes contribute to a more energy-efficient world.
🔹 Example: A typical foam-insulated home in 2025 requires significantly less energy to maintain comfortable indoor temperatures compared to traditional homes, reducing overall utility costs.
2. Durability and Disaster Resistance
Foam homes are designed to withstand harsh weather conditions, fires, and natural disasters, making them an ideal choice for regions prone to hurricanes, tornadoes, and earthquakes.
- Fire-Resistant: Many foam materials are treated with fire-retardant chemicals, reducing the risk of structural fires.
- Hurricane & Tornado-Resistant: ICF and EPS structures can withstand winds up to 250 mph, making them far more resilient than wood-framed homes.
- Earthquake-Resistant: Foam homes have flexibility and shock-absorbing properties, allowing them to endure seismic activity better than rigid materials like concrete or brick.
🔹 Example: After several hurricanes in 2024 devastated traditional wooden homes, communities in coastal areas have turned to ICF foam construction for added resilience.
3. Eco-Friendly & Sustainable
Sustainability is a crucial factor driving the adoption of foam-based construction in 2025. Traditional materials such as concrete and wood contribute to deforestation and CO₂ emissions, whereas foam homes offer a greener alternative.
- Less Material Waste: Foam panels and ICFs generate minimal construction waste, unlike traditional materials that require cutting and trimming.
- Recyclability: Many foam materials used in construction are recyclable, reducing environmental impact.
- Lower Carbon Footprint: Foam homes require fewer resources to manufacture and transport, further decreasing their ecological impact.
🔹 Example: In urban areas focused on net-zero building initiatives, foam-based construction has become a preferred choice due to its low embodied energy and recyclability.
4. Faster and More Affordable Construction
In an era where housing shortages and labor costs continue to rise, foam construction provides a faster and more cost-effective solution.
- Faster Build Time: Foam homes can be constructed in weeks instead of months, thanks to pre-formed panels and modular assembly.
- Lower Labor Costs: The simplicity of foam construction reduces the need for skilled labor, cutting down on overall project expenses.
- Fewer Material Costs: Compared to traditional brick and mortar, foam materials are lighter, easier to transport, and require fewer raw materials.
🔹 Example: Developers in fast-growing cities are using ICF and SIP panel systems to complete entire residential neighborhoods in record time.
5. Improved Indoor Air Quality & Comfort
Foam-based homes contribute to healthier indoor environments by reducing exposure to mold, allergens, and pollutants.
- Moisture Resistance: Foam does not absorb water like wood, reducing the risk of mold and mildew growth.
- Sealed Airflow: Airtight foam insulation prevents dust, allergens, and outdoor pollutants from entering the home.
- Quieter Living: Foam construction provides superior soundproofing, making homes quieter and more comfortable.
🔹 Example: Families with asthma or allergies benefit from the cleaner air and reduced allergens inside foam-insulated homes.
Challenges & Considerations of Foam Homes
Despite their many advantages, foam homes do have some challenges and considerations that homeowners and builders must take into account.
1. Upfront Costs
While foam homes offer long-term energy savings, the initial cost of foam materials can be higher than traditional building materials. However, these costs are quickly offset by lower energy bills and maintenance expenses.
2. Fire Resistance Concerns
Although fire-retardant additives are used in most foam materials, some foam types are still prone to melting at high temperatures. To address this, builders combine foam materials with fire-resistant coatings and reinforcements.
3. Availability & Adoption
Since foam construction is relatively new, some builders may lack experience with foam-based methods, potentially leading to higher labor costs or limited availability in certain regions.
The Future of Foam Homes in 2025 and Beyond
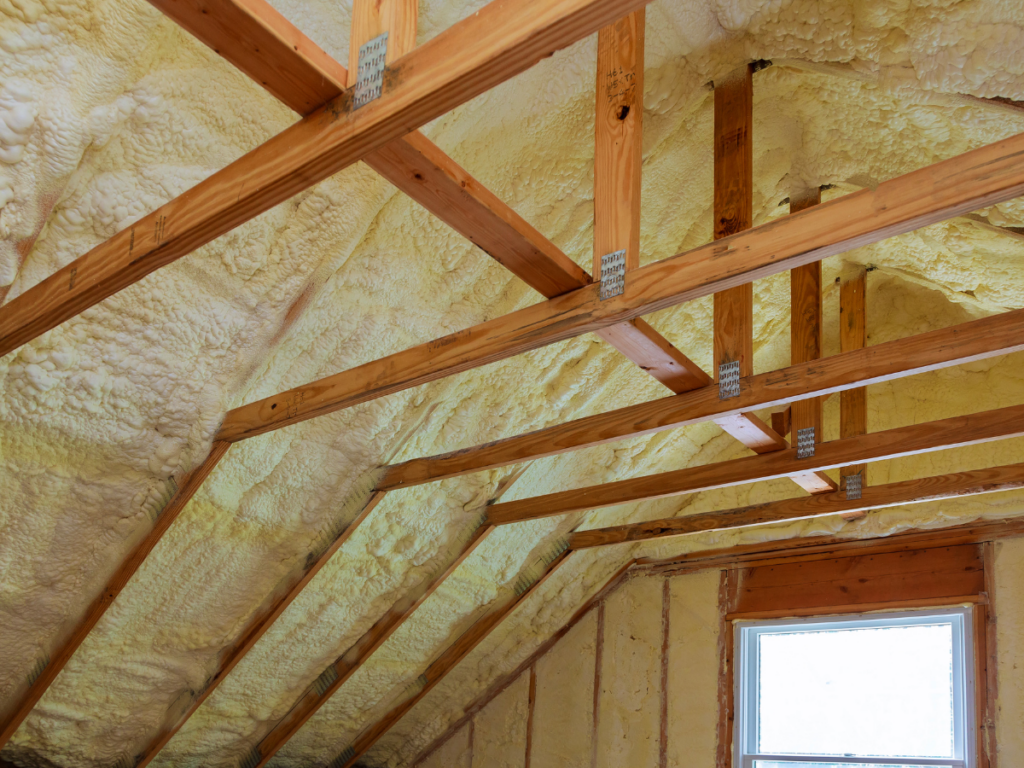
Foam-based construction is expected to become even more widespread as technology advances, costs decrease, and demand for sustainable housing increases. With growing climate change concerns, rising energy costs, and the need for affordable housing, foam homes present a viable, long-term solution for residential and commercial construction.
Predictions for the Future:
- Governments may introduce incentives for foam-based construction due to its environmental benefits.
- Foam homes will become a mainstream option in hurricane-prone and disaster-affected regions.
- 3D printing technology will merge with foam materials, making homebuilding even faster and more customizable.
Conclusion
The emergence of foam homes in 2025 is a testament to the power of innovation, sustainability, and efficiency in modern construction. With advantages such as energy efficiency, disaster resistance, sustainability, and faster construction times, foam-based housing is set to redefine the future of homebuilding. As more builders, architects, and homeowners recognize the benefits, foam homes will continue to grow in popularity, helping create a greener, stronger, and more affordable housing landscape.